SITE ACCESS
Unpacking safety and site access systems
How the system you choose can increase or undermine your project's safety and compliance
Katie O'Mara | Updated on 18 May 2023
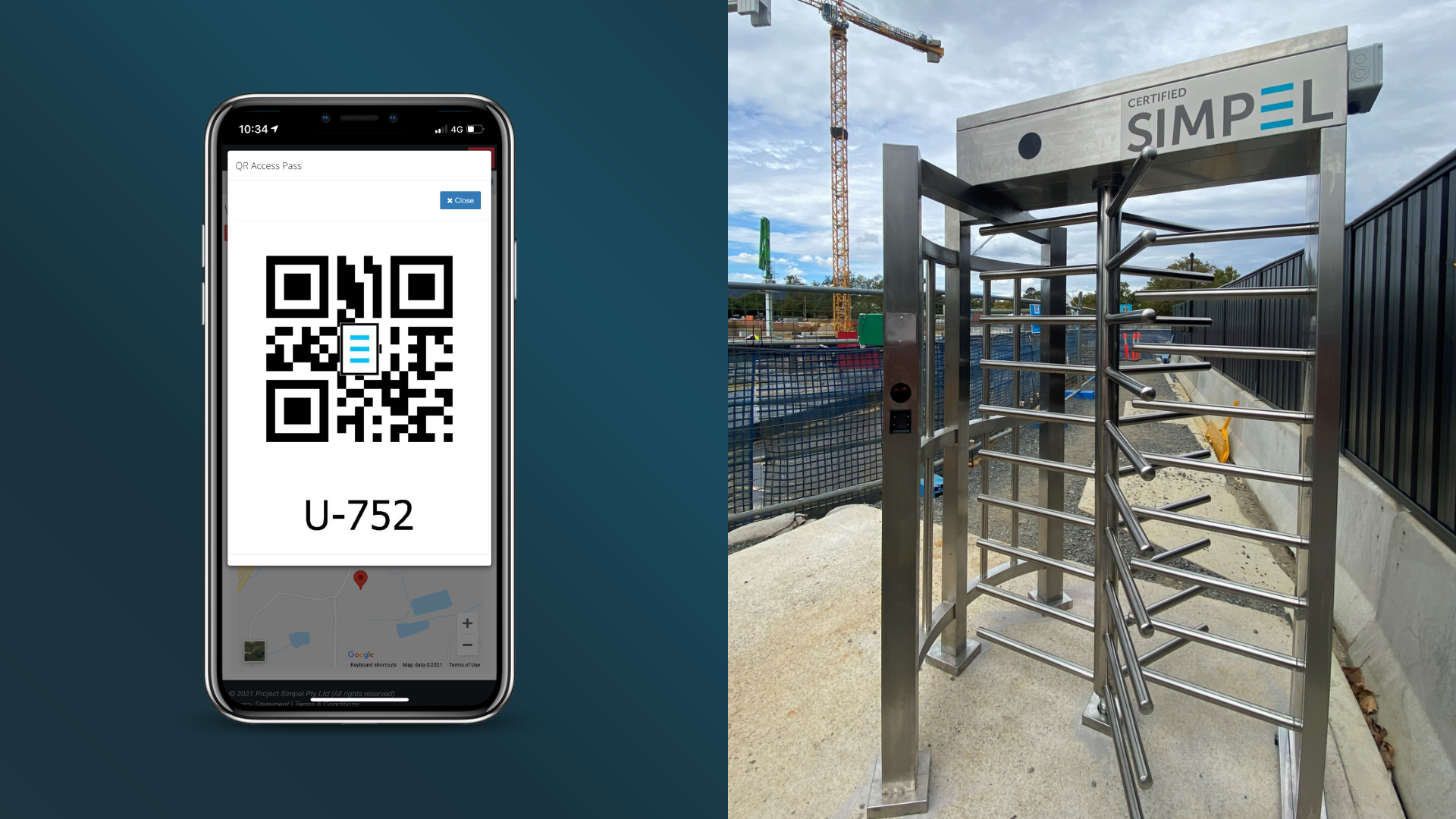
Want to achieve maximum compliance without maximum headache? We review the key functionality to consider when selecting a site access system for your construction project
Physical access control has evolved significantly in recent years as regulatory bodies have introduced new safety checks for workers and visitors entering construction sites. Expanding on use of turnstiles, biometric swing gates and physical sign in at each access point, entering a construction site now requires additional verification of induction status, currency of tickets, completion of SWMS, and more recently - COVID-19 daily declarations and workers vaccination status.
As site access requirements have increased in number and complexity, new systems have also evolved to enable HSEQ managers to more easily manage their implementation. Beyond paper-based systems which are being phased out as the industry transitions to digital, the current approaches vary by the following functional outcomes:
- Process Automation - how much time is saved through elimination of manual processes
- Ease of Implementation - speed of installation and frictionless adoption by workers
- Safety and compliance - degree to which the system enforces compliance and site safety
- Data synchronisation - frequency of encrypted data transmission between the gate and a central database
- Real-time data flow and integrity - the extent to which data registered at the gate can be pushed right through to the central database so it can be used in real-time reporting
HSE Heaven = Automating compliance processes
The goal of HSE management teams should be to eliminate risks and automate as much of the process as possible, alleviating their existing workload and freeing up more time to get back out on site. Process automation is best achieved through a unified gate and software access system that connects a worker’s entry in real-time, with the data on their records, and enables low-touch completion of the verification process.
Software and physical hardware that has been designed as one from the outset, is now proving to be the most effective way to deliver this degree of process automation. But let us tell you why...
A disconnected HSE and site access system will make or break compliance and safety on your project and create rework for your team
We’ve stood on work sites and observed hundreds of installed access systems. We’ve seen first hand the pitfalls and just how much manual effort is required to connect physical and digital components that weren’t designed to work together. It may be that connecting a gate with a third party software system requires a work-around or installation of other apps, use of fobs or even older technology; there may be inaccurate data or absence of real time data, and some even lack the ‘smarts’ to enforce compliance at site entry - permitting a worksite culture that doesn't value or prioritise compliance measures.
Here’s what matters most when selecting site access solutions for your construction site
Frictionless entry/ exit of workers and rapid data validation
Frictionless site movement and a seamless flow of data from sign in, to site management
To increase compliance and maintain efficient movement of workers during peak times, the most effective site access systems are designed to relay immense amounts of encrypted data between gates and software in a matter of milliseconds. Given the volume of workers entering large construction sites, even minor system issues or reduced functionality will result in compounding delays.
An effective site access system should be able to relay data between the gate and software system a minimum of four times per worker per entry.
This workflow requires coordination of numerous system components to relay complex commands and encrypted data packets as they pass through layers of security and are checked against a central database. Completing this process within milliseconds requires a highly orchestrated system that facilitates the flow of data between components without glitches or delays.
The best way to avoid a traffic jam at the gates is to utilise a unified system like Simpel, that transmits a rapid flow of real-time data between gates and software - within milliseconds.
CHECKLIST:
- Does the gate hardware system immediately push/pull data to your site access software system?
- How long does it take for a worker's entry to be validated when they sign in?
- How does the system perform during peak periods? Can it withstand thousands of entry requests at a time?
Compliance automation at the gate
Verify induction status and deny entry to non-compliant or untrained workers
As site compliance remains a priority on every project, ensuring only compliant and trained workers are permitted entry to the site automatically, should be an essential functional outcome of every safety and site access system. Our observations indicate this is not the case.
Why?
Site access systems that rely on third party software or third party gate hardware components are more disparate in their composition and the interfaces between each third party element can behave like a filter, limiting visibility or transmission of core data beyond that point. What this means is that when a worker checks in, the gate hardware system cannot check their compliance status, it can only register their entry; in this example, the gate hardware doesn’t have full visibility of the central software system that stores a worker’s compliance status, as that component was built by a third party.
Unlike competitors, all Simpel’s gate hardware and software components are designed and developed in-house by our Australian team. Simpel’s unified system can complete and verify a worker’s induction and training status automatically and in real-time, and then permit or deny entry to the worker in a matter of milliseconds.
Simpel's systems are able to check compliance such as:
- Is the worker registered?
- Is the worker inducted and permitted to work on the site?
- Has the worker signed the SWMS and safety documentation?
- Is the worker and their company compliance, or has access been suspended or revoked?
- Is the worker seeking access within permitted working hours?
- Is their QR pass activated following their induction approval?
- For biometric access systems - does the worker's profile image match the facial recognition algorithms?
- Has the worker completed a Daily Declaration (COVID or other) and provided acceptable answers to enter the site?
Your team can also be automatically notified when a non-compliant worker attempts to enter your site. They also have the ability to suspend or revoke worker access via the dashboard, at any time.
CHECKLIST:
- Are non-inducted and non-compliant workers prevented from entering the worksite?
- If a non-compliant worker attempts to enter a worksite, will your site team be notified immediately?
Register and receive site movement data in real-time
Up to the minute records of all site movements | Know who is on site, at any time and in real-time
In order to remain fully compliant at a company and worker level, site teams must have the ability to generate real-time records of who is on-site, and who has entered and exited. To achieve this, your hardware must register a worker’s movements and instantly push the data to your site access software where it is easily accessible.
Most site access providers rely on either third party gates or third party software providers to deliver their solution. The danger of relying on third party components is that, as each component was designed in isolation, data flow can be delayed or disrupted as it moves between separate components.
This creates the risk of data lags or corruption which can impair a site’s access to real-time worker movement data.
Know who is on-site in real-time, anytime. A single unified solution which provides a rapid, seamless flow of data between gates and software, ensures all site movements are recorded and available to be exported in real-time.
CHECKLIST:
- Does the operations management software receive real-time site movement data?
- Is your system delivered by a single unified provider and does it integrate with your personnel management software?
- If the system can’t produce real-time data, how does it impact your site compliance?
Gate systems that enforce compliance and meet stringent regulations
Gate systems that allow pass-backs or permit a culture of disregard for compliance are actually failing your HSE team and risking your site security and overall compliance.
To help your team to create a safe and intelligent worksite that meets the latest industry standards, a gate that withstands the rigours of a construction environment, as well as automates and enforces adherence to compliance is crucial for reaching your HSE objectives.
Simpel’s systems are installed at some of Australia’s largest construction sites operated by industry heavyweights including, Multiplex, Lendlease and FDC. These sites host thousands of workers everyday and our access and safety systems facilitate seamless management of tens of thousands of movements, ensuring worksites remain safe and compliant.
Secure your site and enforce compliance at the gates. Simpel has worked closely with industry partners to design biometric flap gates and turnstiles that enforce high compliance and are fully integrated into our software systems, producing a comprehensive site access solution for construction sites of all sizes.
Simpel's built-in features include:
- Anti pass back - allowing only one scan of a QR code for each worker's entry and exit
- Emergency break glass - gates are pre-installed with emergency exit break glass for evacuation management
- Pre-configured wireless communications - all gates are pre-configured with a wireless router and 4G data to allow rapid data flow and a plug and play solution on-site.
CHECKLIST:
- Do the gates have anti-pass back functionality?
- Is the gate compliant with legal regulations and installed with an emergency exit override?
- Does the system enforce compliance at gate entry? How?
Intimate product knowledge from a local support team
An end-to-end site access solution ensures fast and responsive support when you need it
Simpel’s gate hardware, internal componentry and site access and safety module are developed, maintained and rigorously tested in Australia, by our own team. We understand the software and hardware intimately and all support is delivered by our staff. This enables us to diagnose and troubleshoot any issues and get your site up and running quickly.
Built for rough use and flakey wifi providers
Our range of biometric flap gates and brushless stainless steel turnstiles are built for high-traffic sites that receive thousands of workers each day. Our gates undergo regular audits and inspections, with stringent stress testing to ensure they meet technical and regulatory requirements before installation.
4G can be unreliable - We’ve accepted that providers of 4G networks will very occasionally have outages that are beyond our control, so we’ve built-in technical redundancies and multiple fail-safe mechanisms that limit a site’s exposure to outages and send us notifications when they do occur.
If all else fails and the gate can’t re-establish a network connection due to issues with 4G providers, our gates will still permit site entry to existing inducted workers, which would comprise the majority of workers.
CHECKLIST:
- Does your provider use third party apps to connect software and gate hardware? If so, how are problems diagnosed and by who? Will you get passed from one provider to the next?
- Does the router have built-in redundancy to prevent gate disconnection if a network provider (e.g. Vodafone) goes down?
- Does the supplier have automated processes that remotely check the system 24 hours a day to identify potential issues?
- Does your provider have the ability to check and reset your gate hardware remotely?
Continuous innovation delivered at a pace that is unrivalled in the industry
A pivotal difference between a single unified system like Simpel, and a system that relies on components developed by third parties, is the ability to control the entire software development process, to release new functionality and to rapidly respond to new regulatory changes.
At Simpel, we release new software functionality regularly and our R&D team is consistently refining and enhancing our gate hardware and communications technology.
When COVID-19 arrived in Australia, Simpel were the first operations management solution to release new functionality which allowed project sites to:
- automate mandated completion of COVID-19 daily declarations with lock outs for non-compliant workers
- request and securely store vaccination status
All this was validated before the worker was permitted access to a project site. This additional functionality helped to automate new COVID related requirements and to ensure worksites remained safe and highly compliant.
Achieve maximum compliance without maximum headache
Read more about how Simpel's Site Access modules and gate hardware can deliver industry leading compliance, safety and security on your next project